novacontrol – central process control system
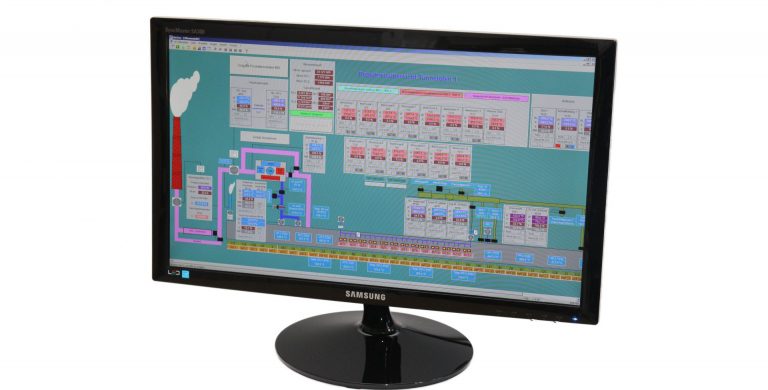
The novacontrol central process control system is special designed for the wide-ranging demands of the ceramic industry. The design supports all functions for operating tunnel kilns and dryers most efficiently.
- a fully configurable control structure, powered by a graphical configuration editor
- easy handling for the operators
- fully automatic control of the thermal process
- maximum support and diagnostics for the operator
- high flexibility in adaptation to customer’s demands
- high reliability
- highest production performance for the dryer and the kiln
- best product quality
- lowest energy consumption and best energy efficiency
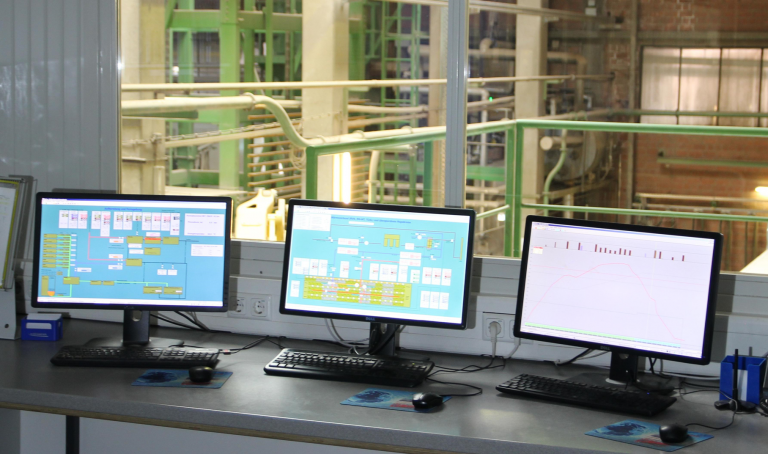
The Technology
novacontrol represents a special SCADA-System.
Special SCADA means: The Supervision, Closed loop Control and Data Acquisition is executed on a single PC for industrial applications.
The interface to the process is realised by a Simatic-S7/1500 PLC, used for fast data acquisition, short pulse outputs and backup controls.
The basic control architecture consists of 3 levels:
- Level 2 novacontrol SCADA-System
- Level 1 PLC-Unit
- Level 0 – Sensors and Actuators in the field/ on the furnace
The ProCeram /novacontrol system is designed for the specific demands of the ceramic industry. The design supports all functions for advanced operation of tunnel kilns and dryers.
The specific functions have been developed to achieve the best controls and supervision for the entire production, including
- Graphical visualization of the plant
- Graphical operation interface, „user-friendly“
- Definition of different user levels with different administrator rights (password-protected)
- Efficient use of drying / firing curves and product recipes
- Up to 1000 different product recipes can be assigned
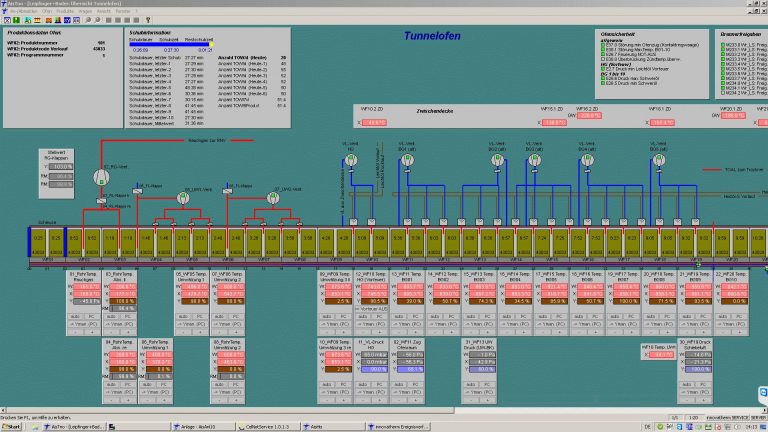
novacontrol is used for
- Control of water and steam dosing in clay preparation and extrusion
- Control of chamber dryers
- Control of continuous dryers
- Control of shuttle kilns
- Control of tunnel kilns
- Control of heat compound between kiln and dryer
- Control of heat exchanger in kiln stack
- Control of thermal flue gas treatment
- Process optimisation (advanced control)
- Energy management for chamber dryers
- Registration of the energy consumption and the production
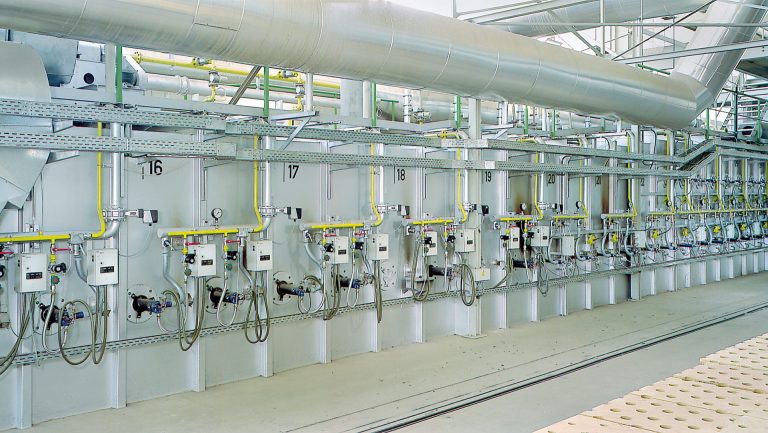
Tunnel kilns
- Product and position related firing programs (resolution is the individual stack on each tunnel car)
- Reduction programs – product and car position related
- O2-control in the preheat zone
- Automatic setpoints for flue gas and push air area
- Definition of up to 100 firing programs
Continuous dryer/ Chamber dryer
- Product, position related and drying time related setpoints for continuous dryers with discontinuous charging
- Automatic setpoints for hot air supply within ranges for operation on lowest possible energy level (!)
- Definition of up to 100 firing/drying programs
- Definition of up to 16 weekly time programs (time based controls)
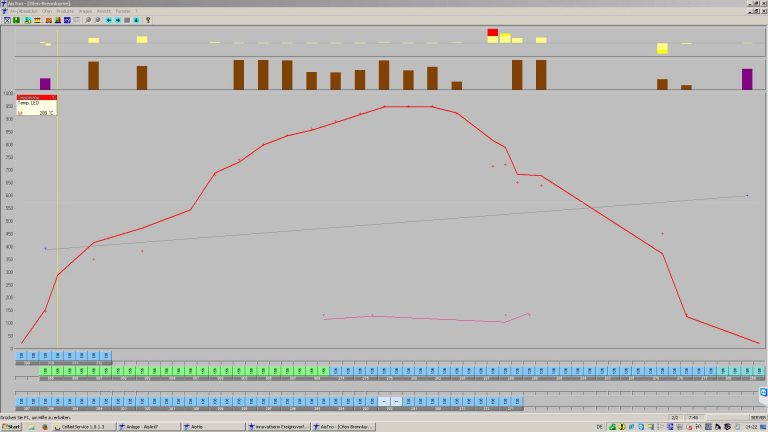
Historical Data
- Individual design of resolution and sample rate for any groups of process values
- Individual design of trends
- Fast display of historical trends
- Historical archive for kiln car curves (= thermal history of each single car stack)
- Historical archive depending on storage size (> 10 years)
Alarm and Message system
- Individual design of alarm and message groups
- Statistical evaluation of alarms and messages
- Alarm- and message archive for 5..10 years
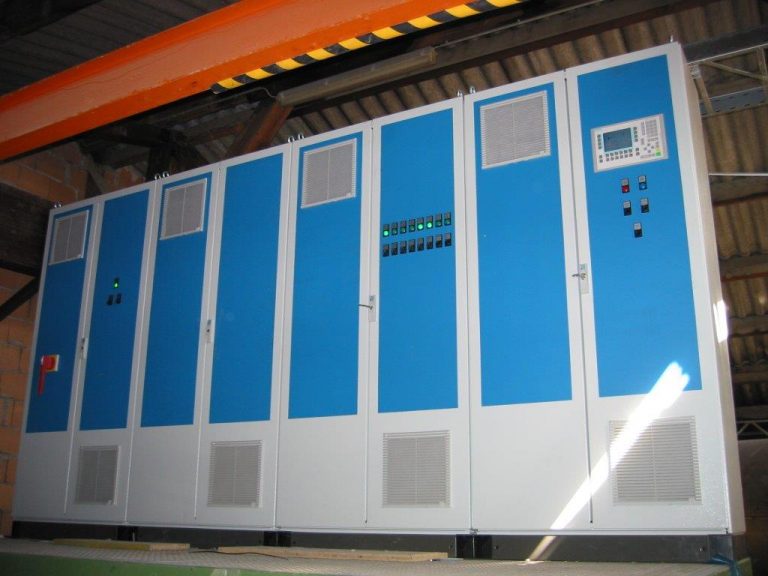
Free configurable control system
- Graphical configuration of the control structure by means of a graphical control editor.
- All control loops may be redefined and / or extended to optimize the control for any specific control loop.
- The control design will be executed graphically in a “virtual control wiring diagram”.
- Software clients for remote access
The operator is able to carry out the following modifications,depending on his user level:
- Change of product data
- Change of control parameters
- Modification of control structures
- Definition of priorities for alarms and messages
- Design of individual visualization screens
- Definition of individual historical trends
- Maintenance and extension of the “on-line language selector”